Experti na hliník
GLEICH Aluminium
Naše produkce
Fokus naší produktové řady je zaměřen na námi vyráběné G.AL® lité hliníkové desky. Ale i válcované hliníkové desky různých slitin a kruhové tyče máme v sortimentu. Přesvědčte se sami!
G.AL® Přesné desky
co máme na mysli přesností
Výběr produktu
G.AL® C250
Přesné desky mají vysokou rozměrovou stálost a vynikající plochost
G.AL® C250 ELOX PLUS
Pro dosažení nejlepších výsledků eloxování
G.AL® C330
vysoká pevnost s vynikající rozměrovou stabilitou
G.AL® lité řezané desky
absolutně rozměrově stabilní během obrábění
Výběr produktu
G.AL® C210R
Hliníkový plech G.AL C210R je vyrobena ze slitiny EN AW-5083, nařezané na všech stranách, a pro celou řadu aplikací vhodných, například v moldmaking Industires.
G.AL® C210R
G.AL® C330R
Čím vyšší pevnosti, šest-strany viděl lité desky ve slitině EN AW-7021 se vyznačuje rozměrovou stabilitou a jeho velmi nízké napětí
G.AL® C330R
G.AL® DYNAMIC
pro dynamicky zatížené součásti
Výběr produktu
G.AL® C210 DYNAMIC
Speciální výrobky pro aplikace pod dynamickým zatížením. Slitina EN AW-5083 – bez mikropórovitosti. Extrémně pnutí.
G.AL® C210 DYNAMIC
G.AL® C330 DYNAMIC
Čím vyšší pevnost DYNAMIC typ slitiny EN AW-7021. prosté mikropórovitosti. Se používá v mnoha pneumatických a hydraulických aplikací.
G.AL® C330 DYNAMIC
GLEICH Aluminium je jedním z předních výrobců na globálním trhu s hliníkovými přesnými deskami díky své celosvětově jedinečné výrobě s vlastním elektricky ovládaným zařízením na tepelné zpracování.
Značka G.AL® se vyznačuje extrémně nízkou deformovatelností, rozměrovou stabilitou a homogenností hliníkových přesných desek a desek na výrobu forem s trvale dobrou kvalitou. G.AL® hliníkové desky se používají ve strojírenství, v laserovém a optickém průmyslu, v lékařských technologiích, při výrobě forem a při výrobě nástrojů.
Vynikající kvalita je dosažena pomocí nejmodernějších, vysoce automatizovaných výrobních zařízení, kde se vyrábějí G.AL® hliníkové lité desky . Jako jeden z mála výrobců s vlastním elektricky ovládaným systémem tepelné pece lze tepelné zpracování řídit velmi přesně, takže mají G.AL® hliníkové lité desky jedinečné vlastnosti z hlediska homogenity, nízkého pnutí a rozměrové stability.
Přířezy na míru!
V našich moderních servisních centrech v České republice, Německu a Polsku řežeme přířezy dle přání zákazníků s nejvyšší přesností .
Naše služby
Od litého hliníkového bloku, přes desky a zákazníkem specifikované přířezy, až po hotové komponenty: tým expertů z GLEICH Aluminium stojí na vaší straně.
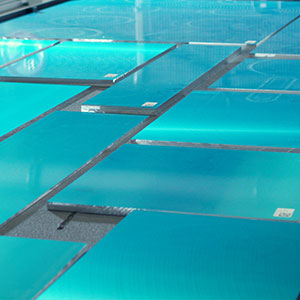
Desky a přířezy z hliníku
Desky a přířezy z hliníku
- velikost desek až do 2.160 x 4.000 mm
- jednotlivé odřezky z 30 x 50 mm
- maximální tloušťka desky až 1.070 mm
- Tolerance pro desky a řízky podle datových listů každého výrobku produkty
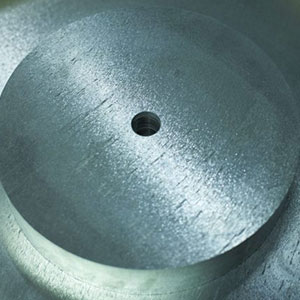
Kruhové řezání a řezání kontur
Kruhové řezání a řezání kontur
Kruhy a kroužky
Řezání pásovou pilou až do 2200 mm + ezání vodním paprskem až do 2160 mm
Řezání obrysů
Řezání laserovým paprskem až do 10 × 2160 × 4000 mm Řezání pásovou pilou až do 600 × 2160 × 4000 mm
Řezání vodním paprskem až do 220 × 1570 × 6000 mm – až do 220 × 2160 × 4000 mm
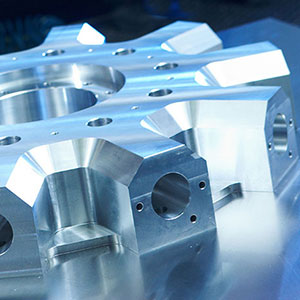
CNC frézování
CNC frézování
Naše CNC výroba se zcela specializuje na hliník. Máme nástroje a obráběcí procesy, které jsou optimálně přizpůsobeny našemu materiálu.
U nás nakupujete přímo od výrobce a máte jednu kontaktní osobu od výroby až po hotový výkresový díl.
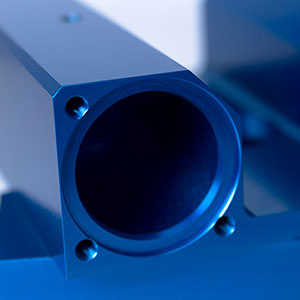
Povrchová úprava
Povrchová úprava
Povrchy hliníkových komponent lze zušlechťovat pomocí různých procesů.
Bez dodatečné povrchové ochrany, která je většinou zajištěna různými eloxovacími procesy, lze vysoce kvalitní povrchy trvale chránit před mechanickým, tepelným a chemickým zatížením.
CNC obráběné díly dle vašich požadavků
Již více jak 30 let se pohybujeme ve světě hliníku. Kromě výroby litých hliníkových desek s nízkým vnitřním pnutím disponujeme vlastním CNC obráběním, které je specializováno na obrábění hliníku.
Spojení našich znalostí o materiálech se znalostmi o CNC obrábění hliníkových slitin nám umožňuje používat optimální materiály společně s optimálními nástroji a obráběcími podmínkami.
Perfektní optika!
Vedle požadavků na povrch materiálu, jako je eloxovatelnost nebo leštitelnost stále rostou požadavky na optický vzhled polotovarů nebo hotových dílů. Těmto požadavkům se stavíme čelem a kombinací našich znalostí z oborů materiálového inženýrství a zpracování povrhů materiálů vám můžeme nabídnout nejlepší možné řešení.
Aluminium Know-How
Profitujte z našich znalostí! Nevíte jaká je nejvhodnější hliníková slitina pro vaší aplikaci? Jaké jsou ideální řezné rychlosti pro jednotlivé slitiny? Proč se lité hliníkové desky nesmí před eloxováním mořit? Pošlete nám své dotazy, rádi vám pomůžeme!
Témat & Znalost
Nedaří se vám při výrobě závitů v hliníkových dílech?
To není třeba!
S procesem přizpůsobeným jednotlivým materiálům lze během krátké chvíle vyrobit odolné vnější i vnitřní závity.
Tepelné zpracování
Společnost GLEICH Aluminium jako jeden z mála výrobců hliníkových bloků disponuje vlastním provozem na tepelné zpracování.
Ale co se přesně během tepelného zpracování odehrává a proč je vlastně potřeba?
Hliník nerezne
Využívání hliníku má mnoho předností.
Jednou z mylně známých předností je, že hliník nerezne. To bohužel neplatí, i hliník může korodovat.
Při využívání našich materiálů je tedy třeba přijmout vhodná opatření pro prevenci nebo omezení koroze.