MIG Schweißen
Das MIG- Schweißen gehört zu den Schutzgasschweißverfahren mit abschmelzender Elektrode. Das Kürzel MIG steht für Metall-Inert-Gas.
Grundsätzliches zum MIG-Schweißen
Das MIG- Schweißen gehört zu den Schutzgasschweißverfahren mit abschmelzender Elektrode. Das Kürzel MIG steht für Metall-Inert-Gas. Bei diesem Verfahren brennt der Lichtbogen zwischen einer mechanisch geförderten Drahtelektrode, die gleichzeitig den Schweißzusatz bildet und dem zu schweißenden Werkstück. Die Drahtelektrode ist als Anode (Pluspol) geschaltet und bewirkt somit die Zerstörung der anhaftenden Aluminiumoxidhaut. Als Schutzgas werden die Gase Helium und Argon bzw. diverse Gemische aus diesen verwendet. Da dieses Verfahren sehr gut mechanisierbar ist, eignet es sich besonders zur Schweißausführung durch Roboter.
Schweißablauf
Das Zünden des Lichtbogens wird durch ein spitzes Drahtende erleichtert. Dies wird durch ein entsprechendes Anschneiden des Drahtes oder ein Drahtfreibrennprogramm am Ende des vorhergehenden Schweißvorganges erreicht. Am Nahtanfang kann es zu Bindefehlern kommen, die durch Anbringen eines Anlaufstückes vermieden werden. Da MIG- Schweißanlagen oft voll mechanisiert oder automatisiert betrieben werden, arbeiten die heutigen Generationen von Anlagen mit einem Zündprogramm. Hierbei setzt die Elektrode kurz auf dem Werkstücke auf wodurch ein Kurzschluss entsteht. Daraufhin wird die Elektrode wieder zurückgezogen, die Spannung steigt und der Lichtbogen zündet. Anschließend wird die Förderrichtung der Drahtelektrode wieder um gerichtet.
Der Brenner sollte senkrecht zur Oberfläche oder unter leichter Neigung von max. 15° geführt werden. Flachere Winkeleinstellungen können zu Lufteinzug in das Schmelzbad und somit zu Porenbildung führen. Bei nachschleppender Brennerführung besteht weiterhin die Gefahr der Schmelzbadüberhitzung. Setzen sich Metallspritzer an der Gasdüse fest kommt es u.U. zu Schutzgasverwirbelungen, die wiederum zu Lufteinzug und Porenbildung führen können.
Ähnlich wie zu Schweißbeginn ist auch zum Ende hin das Anbringen eines Auslaufstückes sinnvoll, um Endkraterrisse zu vermeiden. Ist diese Maßnahme werkstückbedingt nicht umsetzbar, wird der Lichtbogen mit erhöhter Geschwindigkeit über die bereits erstarrte Naht zurückgeführt. Moderne Schweißanlagen verfügen über sogenannte Kraterfüllprogramme, bei denen der Strom und die Drahtzufuhr programmgesteuert gedrosselt werden. Hierbei muss aber das Schutzgas bis zur Erstarrung der Schmelze weiterhin strömen, um Porenbildung durch atmosphärische Einflüsse und möglichen Endkraterrissen vorzubeugen.
Bei geringen Stromstärken wird mit dem Kurzlichtbogen geschweißt. Der Materialübergang findet im Kurzschluss statt, der Lichtbogen erlischt zunächst. Der entstehende Tropfen wird durch den Kurzschlussstrom abgeschnürt, es kommt zur Bildung eines ionisierten Spaltes (durch Metalldämpfe) und der Lichtbogen zündet erneut. Durch das wiederholte Zünden und Erlöschen entsteht ein spritzerbehafteter Schweißvorgang. Durch die geringen Schmelzbäder und die ungünstigen Entgasungsmöglichkeiten wird die Bildung typischer Schweißdefekte, wie Poren und Bindefehler, begünstigt. Mit dem Kurzlichtbogen werden Aluminiumwerkstoffe nur in Ausnahmefällen geschweißt.
Kurzschlussfrei, gleichmäßig und feintropfig ist das Schweißen mit dem Sprühlichtbogen. Hiermit sind bei tiefem Einbrand und somit großer Wärmeeinbringung hohe Abschmelzleistungen möglich. Die Tropfenablösung erfolgt vom flüssigen Elektrodenende durch elektromagnetische Kräfte. Erreicht die Stromdichte in der Drahtelektrode einen bestimmten Wert, der vom Elektrodenwerkstoff und der Leitfähigkeit des Schutzgases abhängt, werden vom Elektrodenende in kurzer Reihenfolge feine Tropfen gelöst und in die Schmelze geschleudert. Die hohen spezifischen Ströme bedingen relativ geringe Drahtelektrodendurchmesser, um die Schweißstromstärke nicht zu hoch ansteigen zu lassen. Da mit geringerem Durchmesser jedoch das Verhältnis Volumen zu Oberfläche der Drahtelektrode sich verschlechtert, kann es zu Porenbildung kommen. Ursache hierfür sind die im Verhältnis vermehrt eingeschleppten (Oberflächen-) Verunreinigungen die aus der Vorbehandlung der Elektroden stammen.
Beim Schweißen mit dem Impulslichtbogen werden ähnliche Kriterien – kurzschlussfrei, feintropfig – wie beim Sprühlichtbogen erreicht. Die Tropfenbildung wird analog wie beim Sprühlichtbogen durch elektromagnetische Kräfte bewirkt. Von großen Vorteil ist die deutlich geringere spezifische Belastung der Drahtelektrode und die Möglichkeit, die Energie (Wärme)- Einbringung sowohl gering zu halten als auch in einem weiten Bereich gut steuern zu können. Somit können sowohl dünne wie auch größere Wanddicken geschweißt werden. Aufgrund der dickeren und damit weniger störanfälligen Elektrode verbessert sich das Verhältnis Elektrodenvolumen zu Elektrodenoberfläche wodurch die Probleme hinsichtlich Porenbildung werden minimiert.
Lichtbogenarten
Beim MIG-Schweißen werden grundsätzlich drei Formen des Werkstoffüberganges im Lichtbogen unterschieden:
Kurzlichtbogen
Bei geringen Stromstärken wird mit dem Kurzlichtbogen geschweißt. Der Materialübergang findet im Kurzschluss statt, der Lichtbogen erlischt zunächst. Der entstehende Tropfen wird durch den Kurzschlussstrom abgeschnürt, es kommt zur Bildung eines ionisierten Spaltes (durch Metalldämpfe) und der Lichtbogen zündet erneut. Durch das wiederholte Zünden und Erlöschen entsteht ein Spritzer behafteter Schweißvorgang. Durch die geringen Schmelzbäder und die ungünstigen Entgasungsmöglichkeiten wird die Bildung typischer Schweißdefekte, wie Poren und Bindefehler, begünstigt. Mit dem Kurzlichtbogen werden Aluminiumwerkstoffe nur in Ausnahmefällen geschweißt.
Sprühlichtbogen
Kurzschlussfrei, gleichmäßig und feintropfig ist das Schweißen mit dem Sprühlichtbogen. Hiermit sind bei tiefem Einbrand und somit großer Wärmeeinbringung hohe Abschmelzleistungen möglich. Die Tropfenablösung erfolgt vom flüssigen Elektrodenende durch elektromagnetische Kräfte. Erreicht die Stromdichte in der Drahtelektrode einen bestimmten Wert, der vom Elektrodenwerkstoff und der Leitfähigkeit des Schutzgases abhängt, werden vom Elektrodenende in kurzer Reihenfolge feine Tropfen gelöst und in die Schmelze geschleudert. Die hohen spezifischen Ströme bedingen relativ geringe Drahtelektrodendurchmesser, um die Schweißstromstärke nicht zu hoch ansteigen zu lassen. Da mit geringerem Durchmesser jedoch das Verhältnis Volumen zu Oberfläche der Drahtelektrode sich verschlechtert, kann es zu Porenbildung kommen. Ursache hierfür sind die im Verhältnis vermehrt eingeschleppten (Oberflächen-) Verunreinigungen die aus der Vorbehandlung der Elektroden stammen.
Impulslichtbogen
Beim Schweißen mit dem Impulslichtbogen werden ähnliche Kriterien – kurzschlussfrei, feintropfig – wie beim Sprühlichtbogen erreicht. Die Tropfenbildung wird analog wie beim Sprühlichtbogen durch elektromagnetische Kräfte bewirkt. Von großen Vorteil ist die deutlich geringere spezifische Belastung der Drahtelektrode und die Möglichkeit, die Energie (Wärme)- Einbringung sowohl gering zu halten als auch in einem weiten Bereich gut steuern zu können. Somit können sowohl dünne wie auch größere Wanddicken geschweißt werden. Aufgrund der dickeren und damit weniger störanfälligen Elektrode verbessert sich das Verhältnis Elektrodenvolumen zu Elektrodenoberfläche wodurch die Probleme hinsichtlich Porenbildung werden minimiert.
nicht gebrochene Stirnkanten, Oxide der Stirnfläche werden nur unvollständig ausgeschwemmt, es bildet sich eine „Wurzelkerbe“
wurzelseitig gebrochenen Stirnkanten, Oxide der Stirnfläche werden vollständig ausgeschwemmt, sehr gute Ausbildung des „Wurzeldurchhanges“
Gleiche Zusammenhänge bezüglich der Stirnseitenvorbereitung treffen ebenso für „Y- Nähte“ zu. Auch hier werden die Stirnseiten wurzelseitig gebrochen. Bei teilautomatisierten Schweißvorgängen und bei größeren Wandstärken kann der Öffnungswinkel bis auf ca. 60° verringert werden.
Für anspruchsvolle, qualitativ hochwertige Schweißverbindungen werden oft „Doppel-Y“ oder sogenannte „X- Nähte“ bevorzugt angewendet. Bei dieser Schweißnahtform besteht die Möglichkeit, die Wurzellage auszukreuzen und gegenzuschweißen. Das wechselseitige Schweißen bewirkt eine deutliche Minimierung der Winkelschrumpfung. Ein Stegabstand ist hierbei oft nicht notwendig.
Vollautomatisierte Schweißprozesse sind beispielsweise in Verbindung mit Robotern gegenüber größeren Toleranzabweichungen bezüglich der Genauigkeiten von Maschinen und Vorrichtungen überaus empfindlich, das Bedienpersonal kann nicht wie bei konventionellen bzw. manuellen Anlagen korrigierend einwirken. Um Abhilfe zu schaffen, sind spezielle Nahtsuch- und Nahtführungssysteme entwickelt worden, die Abweichungen über entsprechende Sensorensysteme (mechanisch- elektrische, optische Systeme und Ausführungen, die den Lichtbogen als Sensor benutzen) erfassen und korrigieren können. Der perfekte Sensor zum vollautomatisierten Roboterschweißen sollte somit direkt an der Schweißstelle messen können (Nachlauffehler verhindern), vorausschauende Messungen ermöglichen und möglichst eine kleine Abmessung aufweisen. Leider ist die Entwicklung solch „idealer / perfekter“ Sensoren, die alle Vorzüge und Eigenschaften beinhalten, noch nicht abgeschlossen, so dass die zur Verfügung stehenden Sensoren auf die jeweilige Schweißaufgabe abzustimmen sind.
Zur deutlichen Erhöhung der Schweißleistungen, also Steigerung von Geschwindigkeit und Abschmelzmenge sowie Spaltüberbrückbarkeit sind einige Verfahrensvarianten des MIG- Schweißens erfolgreich entwickelt worden. Hierbei handelt es sich in mehreren Fällen um Optimierungen hinsichtlich der Zufuhr der Drahtelektroden (MIG- Doppeldrahtschweißen, MIG- Tandemschweißen) bzw. um Veränderungen der Form des Drahtquerschnittes (MIG- Schweißen mit bandförmiger Elektrode). Nachteilig gegenüber den oben genannten Vorteilen wirken sich die aufwändige Gerätetechnik (teilweise zwei Stromquellen), die notwendige Mindestschweißlänge und die Bedingung, diese Prozesse ausschließlich mechanisiert / automatisiert zu betreiben, aus. Weiterhin hat sich der Einsatz bandförmiger Elektroden noch nicht grundsätzlich durchgesetzt, so dass es hinsichtlich der Verfügbarkeit der Elektroden immer wieder Beschaffungsprobleme zu lösen gilt.
In der Entwicklung befindet sich derzeit auch noch ein MIG- Schweißverfahren, welches mit Wechselstrom betrieben werden soll, um mit den dadurch verbundenen Vorteilen auch Materialstärken < 1mm mit geringster Wärmeeinbringung schweißen zu können.
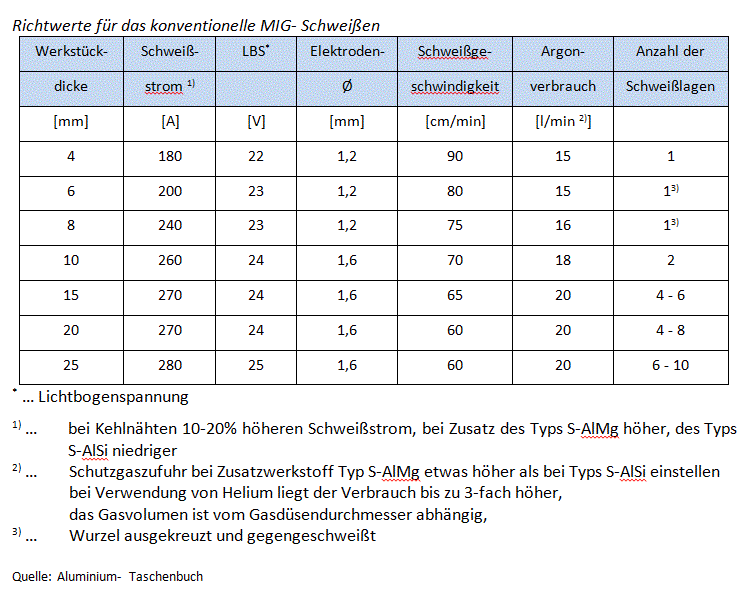
weitere Schweißverfahren für Aluminium
WIG Schweißen
Das WIG- Schweißen zählt zu den Schutzgasschweißverfahren mit nicht abschmelzender Elektrode. Das Kürzel WIG steht für Wolfram-Inert-Gas.
Plasmaschweißen
Das Plasmaschweißen ist es ein Schweißverfahren mit nicht abschmelzender Elektrode. Es stellt eine Weiterentwicklung des WIG-Schweißverfahren dar.
Laserstrahlschweißen
Das Laserstrahlschweißen gehört ebenso wie das Elektronenstrahlschweißen zu der Gruppe der Strahlschweißverfahren.
Elektronenstrahlschweißen
Bei diesem Verfahren wird der Werkstoff durch das Auftreffen hochbeschleunigter Elektronen auf die Werkstückoberfläche geschmolzen.
Rührreibschweißen
Die Besonderheit dieses Verfahrens erklärt sich darin, dass die Fügeverbindung im Solidusbereich des Metalls erfolgt.
weitere Themen zur Zerspanung
Aluminium schweißen
Wie viele andere Metalle können auch Aluminium und seine Legierungen durch Schmelzschweißen miteinander verbunden werden.
Zerspanung von Aluminium
Im Vergleich zu anderen metallischen Konstruktionswerkstoffen gelten Aluminiumwerkstoffe als leicht spanbar. Allerdings sollten die Mindestbedingungen und Parameter bekannt sein.
Frust bei der Gewindeherstellung
Das muss nicht sein!
Mit dem auf den jeweiligen Werkstoff angepassten Verfahren lassen sich im Handumdrehen widerstandsfähige Außen- und Innengewinde herstellen.